Switching to Green
Author: Hannes Rügheimer
In these times of climate change, energy crisis, and inflation, corporate management is almost like a game of Vabanque. Companies must reinvent themselves – and use innovative technologies. Successful examples show how this can be done.
Global energy demand is rising continuously. While it stood at 624 exajoules (the equivalent of around 173 trillion kilowatt hours) in 2021, the International Energy Agency expects it to increase to 673 exajoules by 2030. The output of solar and wind energy, as well as other types of renewable energy generation, is growing rapidly – but the consumption of oil and natural gas also continues to rise. What does all this mean for companies, given the massively rising energy prices but also the increasing urgency to combat climate change? The more energy intensive the business model, the greater the pressure to “go green”. And that often means that companies have to reinvent themselves from the ground up. We took a look around the world for examples where this has already been achieved or is at least well on its way.
Energy company Shell, for example, is building a hydrogen production plant in the port of Rotterdam – in the immediate vicinity of the company’s existing refineries. According to Shell, it will be the largest plant of its kind in Europe. The electrolyzer, which will be housed in a two hectare hall, will have a capacity of 200 megawatts. In 2025, the “Holland Hydrogen I” plant is scheduled go into operation, producing 60 tons of green hydrogen per day with an energy content of over 2,300 megawatt hours, which corresponds to the annual electricity consumption of 650 households.
The electricity required for production will be supplied by an offshore wind farm. Some of the green hydrogen will then in turn be used in Shell’s conventional refinery to produce gasoline, diesel, and jet fuel from mineral oil. But there are also plans to refuel fuel cell trucks on site. The group’s goal is to be completely emission free by 2050.
Green transformation in an energy intensive sector
In the fall of 2021, Germany’s biggest steel group, Thyssenkrupp, produced a large volume of steel with a certified improved life cycle assessment for the very first time. To do so, the company replaced part of the iron ore required for production with sponge iron. This alloy still has an iron content of 92 to 95 percent, but can be melted in blast furnaces with less energy input. The coal saved in the process reduces CO2 emissions. Bernhard Osburg, CEO of the Thyssenkrupp steel division, explained that this reduces the CO2 balance per ton of steel by up to 70 percent.
The first delivery went to a manufacturer of bathroom fixtures – who can thus improve their own carbon footprint. Although the group celebrated this innovation as a milestone in the green transformation of steel production, it also acknowledges that this was only a first step. By 2045, the blast furnaces are planned to be consistently operated with green hydrogen – which would make steel production completely climate-neutral. Other steel manufacturers are also pursuing this goal. After all, the steel sector is currently one of the industries with the highest CO2 emissions.
Domestic biogas production instead of import
But green solutions are not only needed in production. The waste disposal industry also offers opportunities for achieving more climate benefits. For example, the municipal waste disposal company Limeco in Dietikon, Canton Zurich, has been operating Switzerland’s first industrial scale power-to-gas plant since spring 2022. The sewage sludge from local wastewater treatment ends up in a bioreactor. The neighboring waste incineration plant supplies the electricity required to generate climate-neutral methane gas from the sludge. The purified gas is combustible and has the same properties as natural gas. It can therefore be used to heat homes, for example, or stored to generate climate-neutral electricity in gas-fired power plants when photovoltaics reach their limits at night or in winter.
The 10,000 to 15,000 megawatt hours of electricity already generated by waste recycling produce up to 18,000 megawatt-hours of “green” gas. Thomas Peyer of the Swiss municipal utility association Swisspower does the math: If all 30 waste treatment plants in Switzerland were to set up a power-to-gas plant of comparable capacity, together with the biogas already produced in Switzerland today, it would be possible to more or less replace the current import of natural gas from Russia.
From biowaste to biofuel
The Italian oil and energy group Eni (formerly Agip) is not quite as far advanced yet. But the company is operating a pilot plant that produces biofuel from organic waste at its research center in Novara, northern Italy. In pilot operation, this “waste-to-fuel” project uses mainly kitchen waste. Using what is known as hydrothermal liquefaction, the plant converts the moist biomass into a crude oil-like product under high pressure. This can be used, for example, as a crude oil substitute for ship propulsion or refined into higher grade biofuels. The efficiency is an impressive 80 percent. The process also generates up to 60 percent water, which in turn is used in other processes. On a larger scale, the “waste-to-fuel” method could also use sewage sludge, plant waste, or agricultural waste instead of kitchen waste. If this technology were to be implemented consistently throughout Italy, up to six million barrels of crude oil could be saved annually, according to operator Eni. In addition, the process puts waste that would otherwise have to be landfilled or disposed of elsewhere to a valuable and climate neutral use.
Floating wind farms are more efficient
Reducing dependancy on fossil energy and ending it completely as soon as possible is the goal of many other global projects and activities. One of these, for example, can be found 15 kilometers off the coast of Aberdeenshire, Scotland, where the “Kincardine Offshore Windfarm” – currently the largest floating wind farm in the world – operates. A total of six turbines around 200 meters high with 80 meter long rotors use the prevailing strong winds to produce up to 200 gigawatt hours of electricity per year. This amount is enough to supply more than 50,000 Scottish households with electricity. However, with water depths of up to 80 meters, this was only possible by mounting the wind turbines on so-called semi-submersible platforms, which were originally developed for oil and gas rigs. To withstand wind and waves, the platforms, arranged in a triangle, are partially filled with water. A pump system permanently balances this ballast between the three cylinders. In addition, the platforms are anchored to the seabed with cables. In any case, the wind blows more evenly and less turbulently over the sea than on land – which also means less material fatigue and damage to the wind farms.
Experts like Aaron Smith, Chief Commercial Officer of operator Principle Power, point out that up to 80 percent of the world’s sites suitable for wind power are located at sea – in places with comparable water depths. The world’s second largest facility of the kind, located in the Atlantic Ocean, 20 kilometers off the city of Viana do Castelo, Portugal, also makes use of the impressive high-tech design. The “WindFloat Atlantic” offshore wind farm has been supplying electricity to over 60,000 Portuguese households since July 2020.
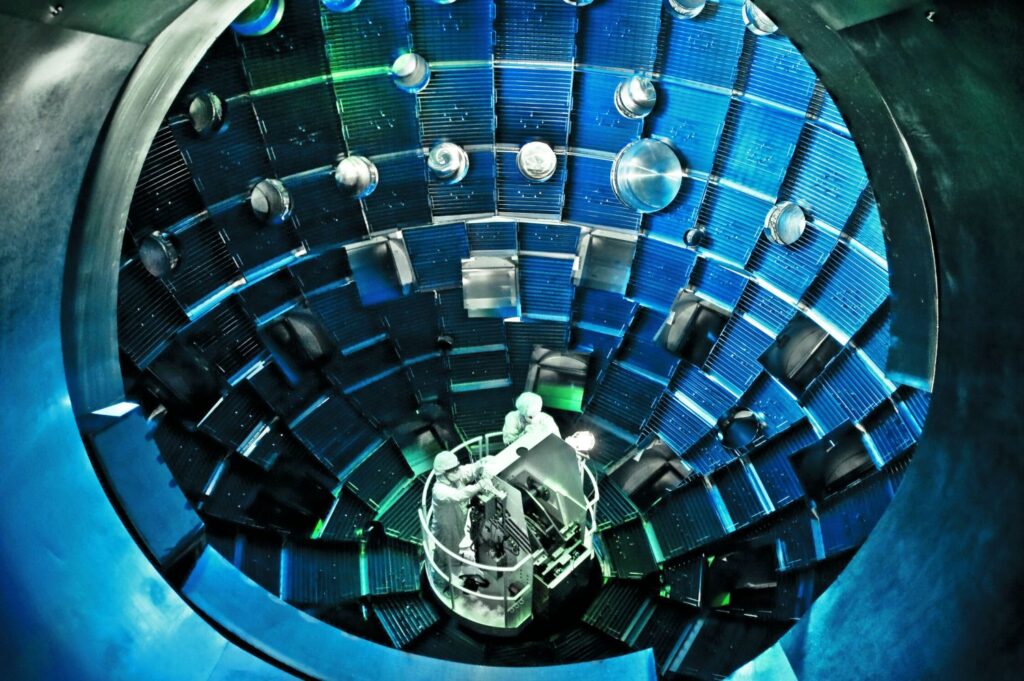
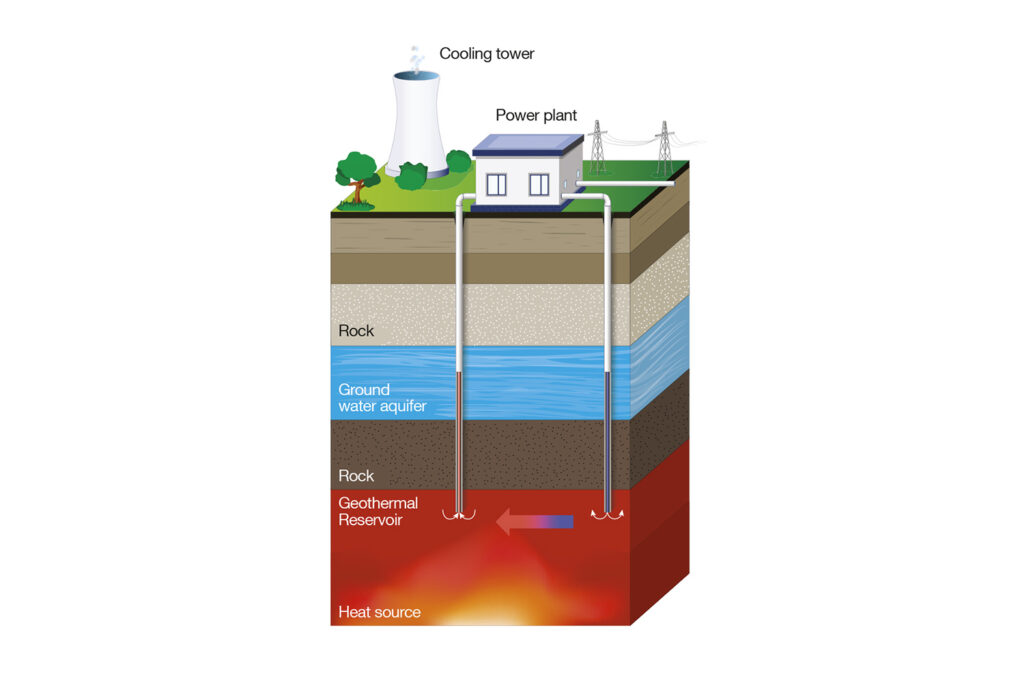
Energy generation with hydropower
But the sea does not only offer new opportunities as a location for generating renewable energies from wind power. Hydropower can also play an important role in sustainable energy generation. In May 2022, the world’s first floating tidal power plant was connected to the grid in the Minas Passage of the Bay of Fundy, Canada, for example. Three power plants, each with six controllable underwater turbines, use the unusually strong local currents with a worldwide unique tidal range reaching up to 16 meters at new and full moon. The concept was realized by the German Schottel Group. A miles-long underwater cable delivers the generated electricity to a transformer station on land. Since summer 2021, the plant has been supplying 4,915 megawatt hours per year, which is enough to supply around 400 Canadian households. There are already plans to scale up the installation, which is currently still declared a demonstration plant.
Microwave technology for ultra deep drilling
On land, on the other hand, initiatives such as Quaise, a US start-up founded in 2018 by researchers at MIT’s Plasma Science and Fusion Center, promise sustainable energy generation through ultra deep geothermal energy. Its founders want to reach unprecedented depths of six to twelve miles and use the heat reservoirs there to supply energy. However, conventional drilling rigs are unsuitable for such deep boreholes. The heat and pressure conditions prevailing several kilometers below the earth’s surface push them to their limits. That is why Quaise wants to use a new type of high frequency microwave technology for the deeper layers of rock. It is intended to literally pulverize or melt the rock. The hot water deposits tapped at great depths could then be used to supply heat directly to households or to generate electricity. The start-up wants to present a functioning system in 2024 and is aiming for commercial use starting in 2026.
Nuclear fusion instead of nuclear fission
If that concept already sounds like a technology from science-fiction movies, then generating energy from nuclear fusion is an even longer way off. But researchers certainly see it as a real option for the future.
As early as 2020, the experimental fusion reactor “Korea Superconducting Tokamak Advanced Research” (“KSTAR”) in Daejeon, South Korea, succeeded in maintaining nuclear fusion for around 20 seconds. Unlike conventional nuclear fission, which splits atomic nuclei in a chain reaction, nuclear fusion fuses atomic nuclei together. This process, which takes place at temperatures of 100 to 180 million degrees Fahrenheit, could provide enormous amounts of energy from simple raw materials such as hydrogen isotopes. But the material load inside the reactors is enormous, and for a long time the experiments consumed more energy than they generated.
But in December 2022, scientists at the US National Ignition Facility (NIF) at Lawrence Livermore National Laboratory in California announced that, for the first time, they had gained more energy from nuclear fusion than they had used – albeit only about 20 percent. “Simply put, this is one of the most impressive scientific achievements of the 21st century,” US Secretary of Energy Jennifer Granholm said about the announcement. Stephane Dujarric, spokesman for the United Nations, added: “It’s an extremely important development that could be of great help in the fight against climate change.”
However, researchers caution against premature expectations. For example, Tony Roulstone, a lecturer in nuclear energy at the UK’s University of Cambridge, explains that the latest result is still far from practical use for energy production. For that to happen, Roulstone says the process would have to produce about twice as much energy as the amount used for it. Optimistic forecasts hope for commercial use in about ten or 15 years, while more pessimistic ones reckon this could take another 30 or 40 years.
Energy demand analysis via auditing
Until that happens, the world as a whole and every company for itself must find viable solutions for their energy demand. A cause for optimism is the fact that the countries with the highest energy consumption (China, USA, and India) are also at the top of the list of countries with the highest installed capacity of renewable energy sources. Individual companies, on the other hand, must be aware that every journey begins with a first step – and that usually means first obtaining an up-to-date and unvarnished overview of all energy requirements and internal energy flows. An energy audit can help.
On top of that, you also need a willingness to innovate and an openness to technology. The examples presented here make it abundantly clear that meeting the challenges of our time with optimism and with a willingness to shape the future is the only way to ensure a sustainable future worth living in – on both a large and small scale.
Saving energy with audits
Energy audits are an effective measure to help companies save energy. In Germany, for example, large companies are obligated to conduct such audits every four years. This obligation applies to all companies that no longer count as small and medium-sized enterprises (SMEs). However, it can also make sense for SMEs to voluntarily carry out energy audits. The exact procedure of an energy audit is defined in the international standard DIN EN 16247-1, for which the requirements are universal.
The audits help identify potential energy savings. They are also a prerequisite, for example, for taking advantage of statutory compensation schemes under the German Renewable Energy Sources Act or similar regulations in many other countries. Essentially, the auditors record all energy flows within the company and rely on current operating data.
A final report summarizes the results and derives an action plan for the company to increase its energy efficiency. The energy audits, which DEKRA offers in several European countries such as Germany, Spain, Portugal, Poland, and Austria, can also be seen as a preliminary stage of an energy management system in accordance with DIN EN ISO 50001.